Ligh weight cal-sil-board
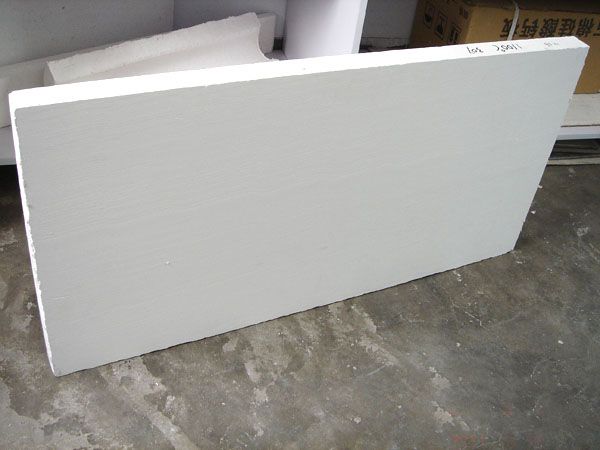
YONGDA—1000C CALCIUM SILICATE INSULATION BOARD
The main constituents of YONGDA-1000C calcium silicate insulation board is Xonotlite and reinforced galss fibre,no asbestos . It is a kind of high efficient energy-saving material with temperature limited 1050 cent-degree.Characterised by low bulk density,high specific strength, superior heat resistance,outstanding thermal insulation,excellent durability, chemical corrosion resistance, easy to be cut by saw and easy installation, calcium silicate can be widely used for the insulation of industrial kiln.
1.PHYSICAL AND CHEMICAL MICROSTRUCTURE ,PRODUCTION,TECHNOLOGY
The main constituent Sonotlite is synthesized through dynamic hydrothermal process using quartz and lime as raw material.. The microstructure crystal looks like a hollow cactus ball and make the board has superior features,unique and irreplaceable.
A.Low thermal conductivity figures—provides top insulation thoughout its temperature range.
B.Good thermal stability—withstand continuous heat up to its full temperature use limit with small linear shrinkage.
C.Light bulk density—low heat storage
D.High mechanical strength— specific strength superior other shaped insulations and retains full integrity at elevated temperatures(excellent creep –resistance).
E.Long service life—no pulverization such like ceramic fibre felt.
F.Safe and clean operation—Free from asbestos,suiphur,and chloride, no toxic carcinogen.
2.APPLICATIONS AND INSTALLATION
Calcium silicate insulation boards are used on all kinds of industrial branches to provide high quality insulating backing.
In kiln system,the insulation board is not exposed to the fire,so the requirement to the insulation material is different from refractory material. Very high use temperature, very high thermal shock resistance and very high mechanical strength are the requirement to refractory material which touch the fire directly.But these item are not important to insulation material. The necessary technical properties for insulation material as following:
A.Low thermal conductivity
B.Low bulk density
C.Gas resistance(CO, NH3,H2 and CH4)
D.Easy cut and installation
Calcium silicate can meet all above requirement and replace other insulation material , it
Is becoming dominant on insulation of industrial kiln.
Areas of application
A.Cement industry: preheaters and cyclone separators, decomposition kiln,tertiary air duct and cooler
B.Nonferrous metallurygical industry: aluminum power calciner and electrolysis groove
C.Petrochemical industry: Splitting furnace,catalytic cracking furnace,petroleum pipeline,underground heat-flooding
D.Metallurgical industry(steel plant): hot-rolling heat furnace,cool-rolling mill set,RH vacuum degassing furnace , smelters,hot deformation and heat treatment plants
E.Power plant:preheat stove ,pipe
F.Glass industry:melting furnace and recuperator,annealing furnace and cooling channels
G.Ceramic industry: chamber and tunnel furnace
3.ACCESSORIES AND INSTALLATION
E.Auxiliary Products
YD—1 High Temp. Adhesive:Blended with water glass to form a mortar for the tight connection between insulationg board with board,also can be used for insulating board and other underdrop with consumption about 3.0kgs/m2.
YD—2 Waterproof Agent: When our insulating board is used with casting material and other monolithic refractories,waterproof agent is painted on the interface with consumption 3.0kgs/m2.
B. Installation tool:Basin and trowel
C. Clean the contact face firstly.
D. YD-1 one portion ,water glass(also named sodium silicate)of about 1-1.5 portion,according to the circumstances surrounding the construction site to determine, thick moderately lean, these two materials fully mixed evenly, you can use.
E. Bonding between the calcium silicate board thickness 1.5-2mm, can be forced extrusion
F. Because our board has very good processability, the general architecture fixer can be used if need.
G.Moisture absorption of calcium silicate board, if do not use water –proof agent, waxed paper and PE film should be considered to be used to separate with casting material .
H.Binder is used the existing service, not to store too much time to avoid hardening crust,will can not be used.
4.SPECIFICATION AND TECHNICAL DATA
A. Chemical Analysis
SiO2……………… 46-48%
CaO ……………… 39—41%
AlO3 …………… 0.39-0.42%
MgO ……………… 0.5-0.7%
Fe2O3 …………… 0.3-0.4%
Na2-K2O ………… 0.9—0.12%
Lgnition loss(mainly H2O)……… 8—11%
B. Our Standard : China Standard :GB/T10699-1998 TYPE-II
Reference Standard: American Standard -ASTM C533-2007 TYPE II
Japan Standard -JIS A9510-1995 NO.1-22
C. TECHNICAL DATA:
ITEM | Unit | YONGDA BRAND | GB/T10699 -1998 TYPE-II | JISA9510-1995 NO.1-22 | ASTM C533-2007 TYPE-II | |||
HCS-20 | HCS-23 | HCS-25 | HCS-27 | |||||
Bulk density | kg/m3 | 200 ±10% | 230 ±10% | 250 ±10% | 270 ±10% | ≤220, ≤270 | ≤220 | ≤352 |
Flexural Strength | Mpa | ≥0.35 | ≥0.50 | ≥0.55 | ≥0.58 | ≥0.30 | ≥0.30 | ≥0.344 |
Cmpressive Strength | Mpa | ≥0.65 | ≥0.85 | ≥0.95 | ≥1.0 | ≥0.50 | ≥0.50 | ≥0.688 |
Thermal Cond. | W/m.k | ≤0.050 +0.00011tt | ≤0.056 +0.00011t | ≤0.058 +0.00011t | ≤0.062 +0.00011t | 0.065 (100±5℃) | ≤0.060 (70±5℃) | ≤0.088 (204±5℃) |
Service Temp.Limit | ℃ | 1000 | 1000 | 1000 | 1000 | 1000 | 1000 | 927 |
Linear Shrinkage | % | ≤2 (1000,16hrs) | ≤2 (1000,16hrs) | ≤2 (1000,16hrs) | ≤2 (1000,16hrs) | ≤2 (1000,16hrs) | ≤2 (1000,3hrs) | ≤2 (927,24hrs) |
D.BLOCK SIZE AND DIMENSIONAL TOLERANCES
Length mm | Width mm | Thickness mm |
400 | 250 | 25-120 |
500 | 500 | 25-120 |
600 | 300 | 25-120 |
1000 | 500 | 25-120 |
1000 | 600 | 25-120 |
1080 | 950 | 50-120 |
1220 | 900 | 50-120 |
E DIMENSIONAL TOLERANCES
YONGDA BRAND | GB/T10699-1998 TYPE-II | ASTM C533-2007 TYPE-II | |
LENGTH | ±2mm | ±4mm | ±3mm |
WIDTH | ±2mm | ±4mm | ±3mm |
THICKNESS | ±2mm | +3mm -1.5mm | ±3mm |
Ligh weight cal-sil-board 本文被阅读 2728 次